5 Common Mistakes in PCB Assembly that can cause PCB failure
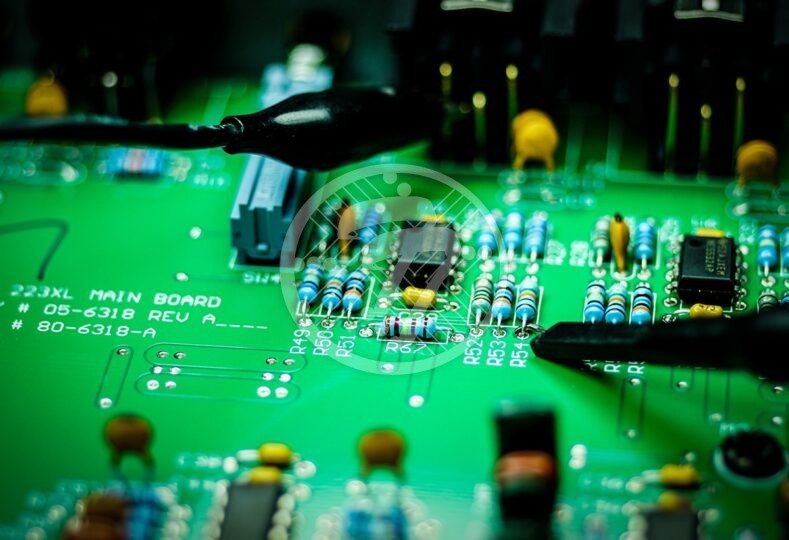
An integral part of most electronic and electrical devices in play nowadays, Printed Circuit Boards (PCB’s) are essentially consists of layers of copper traces connecting together different components to create a complex maze of circuits. The importance of a PCB can be directly gauged by the fact that any errors in its design or assembly can affect the performance and output of the end product. Irrespective of whether you are fabricating PCB’s for a small electrical company or a global technology giant, there are a large number of complications and challenges that can arise during the PCB assembly process that can severely compromise the quality of the final product. Smooth collaboration is a must as far as PCB assembly is concerned, all stakeholders, including designers, engineers, manufacturers and fabricators need to work together to ensure the assembly process runs smoothly and is free of errors. A faulty PCB assembly can end up costing the organization dearly in terms of loss of reputation and returned delivery.
The potential for mistakes during the PCB assembly process exists during any of the process steps, it could be the result of flaws in the technical design itself or it could be the product of operational errors. While there can be any number or reasons for errors in the PCB assembly process, below are 5 of the most common errors mostly responsible for PCB failures.
Reasons for PCB Failure:
Cracking of Flex
Flex cracking is a term used when the excess stress on a ceramic chip capacitor causes the PCB to bend excessively when passed through it. Ceramic chip capacitors are designed to withstand a specific load, when the load generated by a PCB exceeds its maximum capacity, it causes stress on the ceramic chip capacitor which in turn causes the PCB to bend. It is important to use the same or similar load level ceramic chip capacitor during assembly as used during the design phase to ensure the capacitor does not come under stress and cause the PCB to bend or crack leading eventually to PCB performance failure.
Non-marked polarities
Assembling a PCB requires many different components like batteries and diodes which are characterized by polarities. Marking out the polarity of each individual component is very essential to make it easy for assembly engineers to differentiate between anodes and cathodes. In case the polarities are not marked clearly or are wrongly marked, there is very high likelihood of the wrong polarity getting connected to the wrong terminal during the PCB assembly process. Short circuits in PCB are very often caused by wrong connection between polarity and terminal and might even lead the circuit to blow up or at the very least cause some components on the PCB to be completely destroyed.
Inadequate Copper-to-Edge Clearance
Coppers high conductive properties make it an ideal metal for use in electrical and electronic PCB’s. However, as a metal, copper is also highly susceptible to corrosion which can happen if the copper layers get exposed to the environment. This is why copper used in PCB assembly is often coated with other materials like plastic to prevent corrosion. But sometimes during the process of trimming the printed circuit board, the copper coating also gets trimmed, causing the layers beneath to get exposed to the environment increasing the probability of corrosion and malfunctioning of the PCB. This mistake can easily be avoided by ensuring that the space between the edge of the board and the edge of the copper, also known as inner clearance or copper to edge clearance follows specific quality standards.
Plating gaps or voids
An important part of the PCB assembly process is the electroplating deposition process. This process is used to drill holes through the circuit board through which electricity can be carried from one end of the circuit board to the other. Once the holes are drilled, a thin electroless copper layer is added to the board and along the hole walls, which acts as a base for subsequent layers to be added for etching a printed circuit board. Errors during the deposition process can cause holes in copper plating which can prevent the passage of electricity through the hole causing the entire PCB to fail.
Component Misalignment
Each component on a printed circuit board has a specific landing place. Sometimes components shift from their target location during the soldering process by attaching themselves to the molten solder. A misaligned component can disrupt the proper flow of electricity through the circuit board causing the entire PCB to fail. There are only instances when an entire component gets missed during the assembly process leading to system malfunction.
Conclusion
PCB assembly requires skill and expertise, but even then there is scope for error unless you have put adequate quality controls in place at every stage of the PCB assembly process to ensure that one small error in assembly does not cause the entire product to malfunction.
TechnoTronix is one of the kingpins in delivering a well-defined and proven PCB layout and PCB assembly service to the electronics manufacturers. Our main strength lies in the extensive experience and skilled team of experts to provide error less and lead-free PCB assembly and manufacturing solution. You can drop an email to [email protected] or give us a call at 714/630-9200 to solve your queries or to get a quote.