Automotive PCB Assembly Standards: Meeting ISO 26262 and AEC-Q100 Requirements
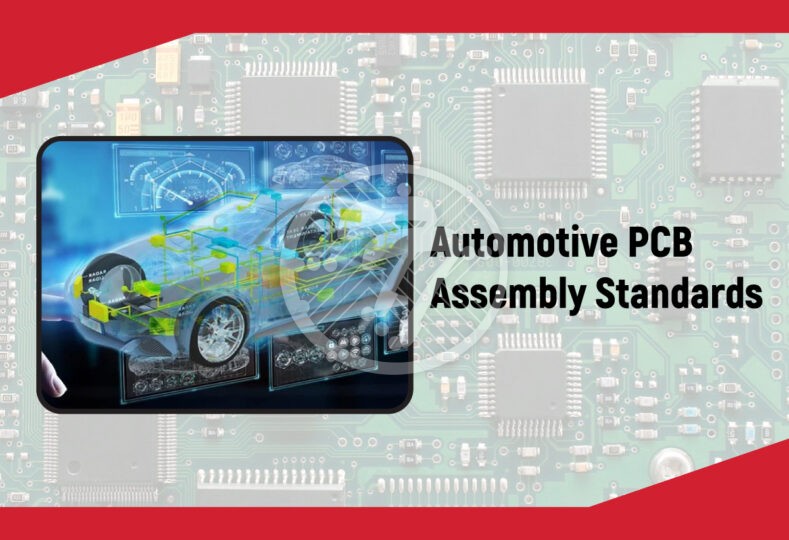
The automotive industry has witnessed a rapid transformation over the past few decades, with electronics playing a crucial role in vehicle performance, safety, and efficiency. Modern automobiles rely on sophisticated electronic control units (ECUs), sensors, and microprocessors to manage everything from engine performance to advanced driver assistance systems (ADAS). Central to these systems are printed circuit boards (PCBs), which serve as the foundation for integrating various electronic components. Given the critical nature of these electronics, ensuring their reliability and safety is paramount.
To meet these stringent requirements, automotive PCBs must comply with rigorous industry standards such as ISO 26262 and AEC-Q100. These standards establish guidelines for functional safety and component reliability, ensuring that automotive electronics can withstand harsh operating conditions and deliver consistent performance. This article explores the significance of these standards, their key requirements, and best practices for achieving compliance in automotive PCB assembly.
Understanding ISO 26262: Functional Safety in Automotive Electronics
ISO 26262 is an international standard developed by the International Organization for Standardization (ISO) specifically for functional safety in road vehicles. It provides a structured approach to minimizing the risk of failures in electrical and electronic systems. The standard covers the entire product lifecycle, including concept development, system design, implementation, verification, validation, and decommissioning.
Key Aspects of ISO 26262 Compliance
- Automotive Safety Integrity Levels (ASIL): One of the fundamental concepts of ISO 26262 is ASIL, which categorizes potential hazards into four levels—ASIL A (lowest) to ASIL D (highest). This classification helps determine the necessary safety measures required to mitigate risks associated with system failures.
- Hazard Analysis and Risk Assessment (HARA): Manufacturers must conduct a thorough hazard analysis to identify potential risks associated with PCB failures. The risk assessment considers factors such as the severity of potential failures, their likelihood, and controllability.
- Safety Requirements Specification: Based on the ASIL classification, specific functional and technical safety requirements are established to guide the PCB design and development process.
- Verification and Validation (V&V): PCBs must undergo extensive testing, including failure mode and effects analysis (FMEA), hardware-in-the-loop (HIL) testing, and software verification, to ensure compliance with ISO 26262 safety goals.
- Documentation and Traceability: ISO 26262 mandates meticulous documentation throughout the development process to ensure traceability and facilitate audits. This includes records of design decisions, test results, and safety assessments.
By adhering to ISO 26262, manufacturers can develop PCBs that minimize safety risks, improve vehicle reliability, and comply with regulatory requirements.
AEC-Q100: Ensuring Reliability of Automotive Electronic Components
In addition to functional safety, automotive PCBs must incorporate highly reliable electronic components capable of withstanding harsh environmental conditions such as temperature fluctuations, mechanical vibrations, and electrical surges. The Automotive Electronics Council (AEC) developed the AEC-Q100 standard to define stress test qualification requirements for integrated circuits (ICs) used in automotive applications.
Key Aspects of AEC-Q100 Compliance
- Stress Test Qualification: AEC-Q100 mandates rigorous stress testing for electronic components to simulate real-world automotive conditions. These tests evaluate parameters such as temperature cycling, high-temperature operating life (HTOL), and humidity resistance.
- Failure Mechanism Analysis: Components must undergo failure mode analysis to identify potential weaknesses and improve their design. This helps in ensuring long-term reliability and reducing field failures.
- Temperature Grading: Automotive environments experience extreme temperature variations, from sub-zero conditions to high-heat engine compartments. AEC-Q100 classifies components based on their operational temperature ranges, ensuring that only suitable parts are used in specific applications.
- Electrostatic Discharge (ESD) and Latch-Up Testing: The standard includes testing for ESD sensitivity and latch-up conditions to prevent electrical damage to components during handling and operation.
Integrating ISO 26262 and AEC-Q100 in Automotive PCB Assembly
Meeting both ISO 26262 and AEC-Q100 requirements requires a holistic approach that encompasses component selection, design methodology, testing protocols, and manufacturing processes. Below are key considerations for achieving compliance:
-
Component Selection
Selecting AEC-Q100 qualified components ensures that all electronic parts integrated into the PCB can withstand automotive-grade environmental stresses. This includes choosing ICs, resistors, capacitors, and other semiconductors that meet temperature and durability criteria.
-
Design for Reliability
PCB designers must incorporate robust design principles to enhance the reliability and safety of automotive electronics. This includes:
- Implementing redundant circuits for critical functions.
- Using high-quality, temperature-resistant materials.
- Ensuring proper grounding and shielding to mitigate electromagnetic interference (EMI).
-
Testing and Validation
Comprehensive testing protocols must be implemented to validate the performance and safety of PCBs. These include:
- Environmental Stress Testing: Simulating real-world conditions such as thermal cycling, humidity exposure, and mechanical shocks.
- Electrical Performance Testing: Verifying signal integrity, power distribution, and fault tolerance.
- Safety Analysis: Conducting FMEA and fault tree analysis (FTA) to identify potential failure points and corrective measures.
-
Manufacturing and Quality Control
Automotive PCBs must be manufactured under stringent quality control measures, including:
- Adhering to IPC-A-610 Class 3 standards for high-reliability electronics.
- Implementing automated optical inspection (AOI) and X-ray inspection for defect detection.
- Conducting in-circuit testing (ICT) and functional testing before deployment.
-
Documentation and Compliance Reporting
Manufacturers must maintain detailed records of design decisions, testing procedures, and compliance certifications to demonstrate adherence to ISO 26262 and AEC-Q100. Proper documentation also facilitates supplier audits and regulatory approvals.
Challenges in Achieving Compliance
While meeting ISO 26262 and AEC-Q100 standards is crucial, manufacturers often face challenges such as:
- Complexity of Standards: Understanding and implementing the intricate requirements of these standards requires specialized expertise.
- Cost Implications: Achieving compliance involves additional testing, certification, and component sourcing costs.
- Supply Chain Management: Ensuring that suppliers provide certified, high-quality components adds another layer of complexity.
Best Practices for Success
To effectively navigate these challenges, companies should adopt the following best practices:
- Early Integration of Safety and Reliability Considerations: Addressing safety and reliability during the initial design phase prevents costly redesigns later in the development process.
- Cross-Functional Collaboration: Encouraging collaboration between engineering, quality assurance, and supply chain teams ensures a unified approach to compliance.
- Continuous Improvement: Regularly updating processes based on field data, test results, and regulatory changes helps maintain high standards of safety and reliability.
Conclusion
Automotive PCB assembly must meet stringent safety and reliability standards to ensure optimal vehicle performance and passenger safety. Compliance with ISO 26262 ensures that electronic systems are designed with functional safety in mind, while adherence to AEC-Q100 guarantees the use of high-reliability components. By integrating these standards into the design, testing, and manufacturing processes, automotive electronics manufacturers can enhance product quality, meet industry regulations, and build trust with customers. As automotive technology continues to evolve, maintaining a strong commitment to these standards will be crucial for innovation and long-term success in the industry.
Ensuring compliance with ISO 26262 and AEC-Q100 is crucial for the safety and reliability of automotive PCB assemblies. At Technotronix, we specialize in delivering high-quality, standards-compliant PCB solutions for the automotive industry. Partner with us for precision, durability, and cutting-edge manufacturing expertise. Contact us today to discuss your project!