What are the specific requirements of Bill of Materials (BOM) for cable harness assembly manufacturing?
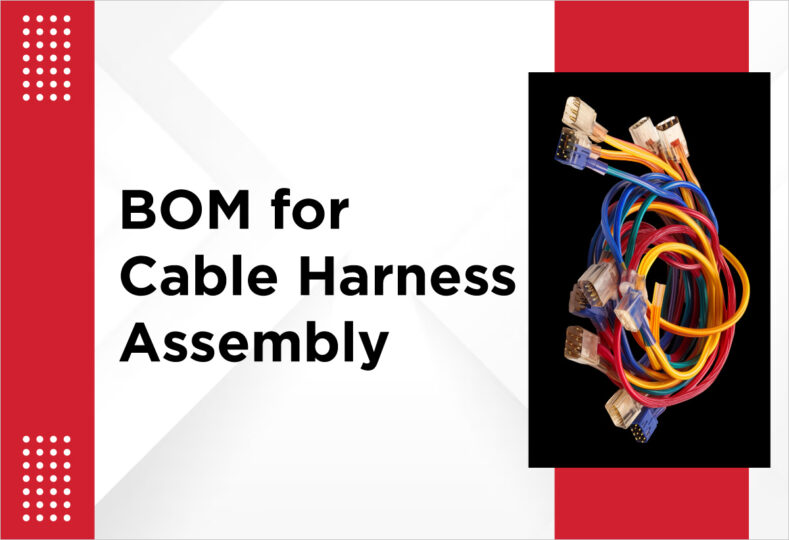
In the manufacturing of cable harness assemblies, the Bill of Materials (BOM) is a critical document that details all the components, materials, and assemblies required to produce a final product. An efficient and cost-effective manufacturing process relies on a well-structured BOM. It provides a comprehensive guide for sourcing materials, managing inventory, and facilitating communication between different departments. This article will explore the specific requirements of a BOM needed for cable harness assembly manufacturing, highlighting its importance and key components.
The importance of a BOM in cable harness assembly
A BOM is more than just a list of parts; it is a comprehensive document that provides detailed information about each component required for the manufacturing process. This detailed document acts like a recipe, outlining the exact specifications and quantities of materials needed, much like a recipe provides the ingredients and instructions for baking cookies. A BOM serves multiple purposes in the manufacturing of cable harness assemblies:
- Material Management: It lists all materials required, helping to maintain optimal inventory levels and avoid shortages or excesses.
- Cost Estimation: By detailing all components and quantities, a BOM aids in accurate cost calculation, which is crucial for pricing and budgeting.
- Production Planning: It provides a blueprint for the assembly process, ensuring that all necessary parts are available, and that the assembly can proceed without interruptions.
- Quality Control: A BOM helps ensure that the correct components are used, maintaining the quality and consistency of the final product.
- Regulatory Compliance: In industries with stringent regulations, a BOM helps ensure that all materials and processes comply with relevant standards
Key Components of a BOM for Cable Harness Assembly
A BOM for cable harness assembly manufacturing typically includes several key components:
- Part Number: A unique identifier for each component, which simplifies tracking and management.
- Description: A detailed description of each component, including specifications such as dimensions, materials, and electrical properties.
- Assembled quantity: The number of components required.
- Unit of Measure: The measurement unit used to quantify each component (e.g., pieces, meters).
- Manufacturer’s Part Number: The part number assigned by the component’s manufacturer, who helps in sourcing and verification.
- Supplier Information: Details of the suppliers from whom the components can be sourced, including contact information and lead times.
- Component Image: Visual representation of each component, which aids in identification and assembly.
- Assembly Instructions: Specific instructions on how each component should be assembled, including any special handling or installation requirements.
Detailed Requirements for Cable Harness Assembly BOM
To create an effective BOM for cable harness assembly, certain specific requirements need to be met:
-
Comprehensive Component Listing
A cable harness assembly BOM must include all components, no matter how small or seemingly insignificant. This includes:
- Wires and Cables: Detailed information on wire types, lengths, gauges, and insulation materials.
- Connectors: Specifications for connectors, including type, pin configuration, and mating requirements.
- Terminals: Types of terminals used, their material, and crimping specifications.
- Protective Components: Items such as sleeves, grommets, and heat shrink tubing, including their sizes and materials.
- Mounting Hardware: Details of any brackets, clamps, or fasteners required to secure the harness in place.
- Labels and Markers: Information on labeling and marking components for identification and compliance purposes.
-
Material Specifications
For each component, the BOM should include precise material specifications. This ensures that the correct materials are used, which is crucial for performance, safety, and compliance. Material specifications should cover:
- Electrical Properties: Conductivity, resistance, and insulation ratings.
- Mechanical Properties: Tensile strength, flexibility, and durability.
- Environmental Resistance: Resistance to factors such as temperature, moisture, chemicals, and UV exposure.
-
Quantities and Units of Measure
Accurate quantities and appropriate units of measure are essential for effective material management. The BOM should specify the exact number of each component needed, along with the unit of measure (e.g., meters for cables, pieces for connectors). This helps in precise inventory management and cost estimation.
-
Source and Supplier Details
To streamline procurement, the Bill of Materials (BOM) should include detailed information about the sources and suppliers of each component. This should cover:
- Supplier Names: Names of approved suppliers for each component.
- Contact Information: Contact details for procurement and order placement.
- Lead Times: Estimated lead times for each component, which aids in production planning.
- Alternative Suppliers: Information on alternative suppliers in case of supply chain disruptions.
-
Assembly Instructions and Quality Control
The BOM should include detailed assembly instructions to guide the manufacturing process. This ensures that components are assembled correctly and efficiently. Additionally, quality control checks should be integrated into the instructions, specifying:
- Inspection Points: Key stages in the assembly process where quality checks are required.
- Testing Requirements: Electrical and mechanical tests that need to be performed on the assembled harness.
- Acceptance Criteria: Standards and criteria that the final product must meet to be considered acceptable.
-
Regulatory and Compliance Information
In industries such as automotive, aerospace, and medical devices, regulatory compliance is critical. The BOM should include information on relevant standards and regulations, ensuring that all components and processes comply. This may cover:
- Safety Standards: Compliance with electrical and fire safety standards.
- Environmental Regulations: Adherence to regulations on hazardous materials (e.g., RoHS, REACH).
- Industry-Specific Standards: Compliance with industry-specific standards (e.g., IPC/WHMA-A-620 for cable and wire harness assemblies).
Future Trends in BOM Management
As technology evolves, so do the tools and methods for managing BOMs. Innovations such as flexible PCBs, High-Density Interconnect (HDI) technology, and substrate-like PCBs (SLP) are changing the landscape of cable harness manufacturing. These advancements allow for smaller, more efficient designs, which in turn require more precise and detailed BOMs.
Additionally, the use of Internet of Things (IoT) and Artificial Intelligence (AI) in manufacturing is enhancing the accuracy and efficiency of BOM management. AI can help identify potential issues before they arise, while IoT enables real-time tracking of components and materials.
Sustainability in Cable Harness Manufacturing
Sustainability is becoming increasingly important in manufacturing. Innovative materials, such as water-soluble PCBs like Soluboard, are reducing waste and environmental impact. As manufacturers strive to meet sustainability goals, BOMs will play a critical role in ensuring that materials and processes align with these objectives.
Conclusion
A comprehensive and detailed BOM is indispensable for the successful manufacturing of cable harness assemblies. It ensures that all necessary components are accounted for, facilitates efficient production planning, and helps maintain high-quality standards. By including all relevant information—such as part numbers, descriptions, quantities, material specifications, supplier details, assembly instructions, and regulatory compliance—the BOM becomes a crucial tool in the manufacturing process. Properly managed, a BOM not only streamlines operations but also contributes to cost savings, improved quality, and enhanced overall efficiency in cable harness assembly manufacturing.
At Technotronix, we have more than 40 years of experience in manufacturing and assembling industry-leading products. Equipped with state-of-the-art equipment and skilled personnel, we offer products to meet your requirements. TechnoTronix is a leading cable and wire harness assembly manufacturer who will deliver ample of smart solutions related to PCBs.