Surface Mount vs Through Hole – Which one is the best for your next project?
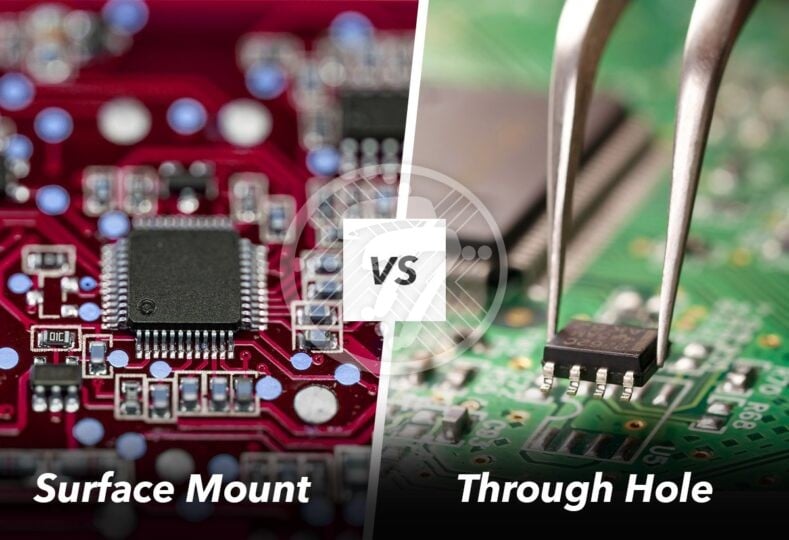
Today, all modern electronic devices contain printed circuit boards (PCB) on which various electronic components like capacitors, resistors, integrated circuits, transformers, and so on are connected. And there have been two primary methods for mounting these electrical components onto the PCBs – surface mount and through-hole.
There has been a never-ending debate over which type of components should be used – surface mount or through-hole. If you face are as puzzled as everyone else, you are at the right place. In this article, we cover some of the basic differences between SMT and through-hole and help you make the right choice for your next project.
What are SMT and through-hole technologies?
Initially, through-hole parts were the only known components that were prevailing when printed circuit boards came into production. With time, Surface Mount Technology (SMT) saw the light of the day and became popular. Now, it is the most dominant component type used in the PCBs.
In the surface mount technology (SMT) method, you mount the components directly on the surface of the PCB using a solder. And the majority of electronic hardware manufactured today has PCBs that are assembled using this SMT method.
In the through-hole method, you take a bare PCB and drill holes onto it. The leads of the components are inserted here. With the rise of surface mount technology assembly, this process may seem to be obsolete, but TMT has its own benefits and still relevant.
Manufacturing Differences
There are some notable manufacturing differences between SMT and through-hole components.
There are two ways for soldering components onto the printed circuit boards –
- Wave solder
- Solder reflows
Although not a hard-and-fast rule, but most of the SMT components are solder reflowed, while through-hole components are wave soldered. In the through-hole PCB assembly technique, even if the components are inserted into the holes that are drilled, the circuit boards are run through a wave soldering for forming a strong solder joint. Quite often, through-hole parts are manually inserted.
For SMT components, solder paste is directly applied to the pads keeping the leads of the components in one place. The solder paste reflows when the PCB runs through the specialized oven. Here, a solid solder joint is formed. If you are using a mixed type, then a mixture of both wave solder and solder reflow is required. There are automated pick-and-place machines that are readily available that can handle a variety of components in a reliable fashion.
Benefits of SMT and Through-hole
Let us understand why SMT component types are used frequently –
Size – SMT components or parts are small or miniature by default. There is no need for drilling down the holes. This looks clean and attractive especially in the age wherein electronics come with smaller board sizes.
Availability – Today, SMT has taken over the through-hole components. They are smaller and replaced the through-hole parts like resistors, capacitors, etc.
Performance – The use of smaller parts in SMT makes the electrical signals travel through a less distance. This reduces the signal flight time as well. Hence SMT components offer better electrical performance than through-hole components.
Cost-effective – SMT parts are usually less expensive than the through-hole counterparts.
Let’s quickly look into the benefits of through-hole parts as well.
Availability – If you need larger parts that are used in high-power applications, it may be difficult to find an SMT equivalent part. Through-hole parts are readily available.
Strength – If there is constant stress that the parts have to go through, SMT solder joints may break. In such cases, components like connectors, switches, and other interface parts need the strength that is effectively provided from the leads soldered into a drilled hole.
Power – SMT is not a good option for high power circuits as it is difficult for SMT soldering to achieve strong solder joint. Hence a through-hole technique offers a more robust mechanical strength for thermal, high voltage, and mechanical stability.
Other differences between SMT and through-hole
In SMT, more components can be mounted on the circuit board as the SMT components are smaller in size. Also, both sides of the board can be utilized. Space issues won’t be a problem which is usually the case in the through-hole process. You can have smaller and lighter designs that are powerful and faster through the SMT process.
If you wish to have high production volumes, then go for the SMT process as it offers a lower cost per unit.
Even the pin count or component lead count on SMT is large when compared to the through-hole process.
But SMT Printed circuit boards needs some heavy capital investment for setting up the machinery and production process. This is significantly larger than the through-hole process.
Also, the level of skill, design, technology, and production required for implementing the SMT is advanced than the through-hole.
SMT Or Through Hole?
At the outset with automated equipment, smaller size components, and cost-effectiveness, SMT components may seem to be the best choices for your printed circuit board designs. But don’t make such a mistake and jump to any conclusion. Both the component styles are equally important. These advantages do not imply the end of through-hole components.
Most of the integrated circuits go for the SMT package. However, for connectors, switches, or mechanical power parts, the standard way is to use through-hole parts. Also, legacy boards still use through-hole parts to fulfil your exact requirements. The robust through-hole parts are going to be of utility for a longer time.
Conclusion
A contest between surface mount vs through hole on the circuit board has been a long drawn one. There is no clear winner in this debate as each component type serves a different function and most of the time, the majority of the PCBs prefer a mixed type that involves both types. The key thing is to choose the right part for your specific project. The next important thing is to find the right PCB Assembly services. Technotronix has over 4 decades of experience and equipment to manufacture both types of component packages efficiently. We ensure the highest level of quality for your circuit board in both cases.