10 Benefits of Choosing Dedicated PCB Assembly Partner in USA
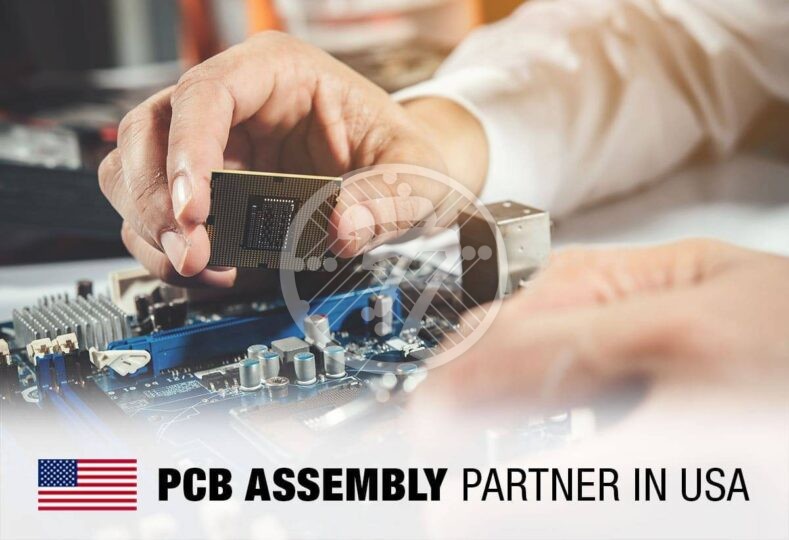
In business, if there is one rule that works, it is to focus on what you do best and to outsource the other services to experts in the domain, for you to reap a competitive advantage. This is especially true in the electronics business where products are becoming increasingly compact and complex. It is only when you can take advantage of the latest printed circuit board assembly that you can offer a state-of-the-art product. This is the exact reason why you stand to gain tremendously when it comes to choosing a dedicated PCB Assembly partner.
Here are some of the top reasons to choose a dedicated printed circuit board assembly partner:
Design efficiency
The job of a PCB Assembly partner does not just include managing the PCB Assembly process. In fact it actually starts at the PCB design stage. With their experience and expertise they can point out issues, if any, at the design stage itself. In turn what it will do for you is to ensure that you have an efficient design and that you do not have to face costly errors and delays at a later date when you are ready to go-to-market. A PCB Assembly partner, on account of their knowledge and expertise in handling many such projects can proactively point out any improvement areas at the design stage itself. It will help for them to take a look at your plans so any flaws can be addressed early. Check out top 8 Things to Help in PCB board assembly That You Must Know.
Time-to-market
A direct corollary of the above is the reduced time-to-market especially since that can be a big competitive advantage in today’s day and age. Partnering with a professional printed circuit board assembly partner ensures that since any issues are brought to light early, there isn’t any wastage of time. Also a professional partner will stick to deadlines and therefore not cause a vicious cycle of delay by delaying their deliverables.
Takes away the need for multiple prototypes
Having put his expertise into your design at an early stage, a PCB Assembly partner takes away the need to create multiple prototypes. Now that can result in a host of savings in terms of time, effort and money.
Latest technology
Another significant advantage of an assembly partner is that he brings to the table the latest design and manufacturing technology. In turn, this ensures that the boards are designed with advanced processes as well as with precision.
Cost advantage
On account of the scale of their work and the relationship they have with suppliers, PCB Assembly companies have a distinct advantage when it comes to offering optimal costs. In turn, of course, it helps you price your product competitively. Contrast this with a situation where you have to procure supplies yourself. Not only does it result in wastage of a lot of time, odds are that you will not be able to match the costs. Visit the blog to of Simple Ways to Reduce PCB Assembly Cost.
Ease of pricing
With the PCB Assembly partner giving you one firm cost estimate, it becomes easy for you to price your final product and not be constrained by changing cost estimates, which can render your product pricing awry.
Manage Supply Chain
What the PCB Assembly partner, in effect, helps you to do, is to manage your supply chain with ease. You no longer have to contend with multiple partners and spend your time and energy on them. The issue of dealing with multiple partners also is that delay on any one front can lead to a cascading effect and derail your timelines.
Save on Repairs
When you procure supplies on your own, troubleshooting and repair tends to consume a lot of your time not to mention the costs that you incur when it comes to faulty units. With a PCB Assembly partner, on the other hand, you can rest assured that warranty replacements are an issue that he has to contend with.
Time to focus on your core competence
Should you choose not to go with a PCB Assembly partner, the biggest toll that is taken is on your time. You tend to spend a lot of time going back and forth on logistical issues and aren’t able to focus on your core competence, when in fact focusing on it will give you a significant advantage in the market place.
Range of services
A PCB Board Assembly Partner also offers you a range of services including but not limited to:
- Data management
- Reverse engineering
- Compliance testing and more
It is therefore prudent to seek out a professional partner that can help you harness a host of advantages. In choosing the right PCB Assembly partner, do ensure that you do a due diligence to identify partner strengths. It may be a good idea to look up their list of satisfied customers as also to get their testimonial.
Technotronix inc is a California based PCB Assembly Company offering dedicated PCB assembly, PCB prototyping, PCB fabrication, PCB box build, turnkey PCB assembly, PCB material management, flexible PCB, SMT and more services as per customer requirements and specification.
In case if you have any questions, please feel free to contact us via email at [email protected] or call us at 714/630-9200.