Significant Fuss And Ways To Mitigate Moisture – A Catastrophe to mechanism of PCB Assembly
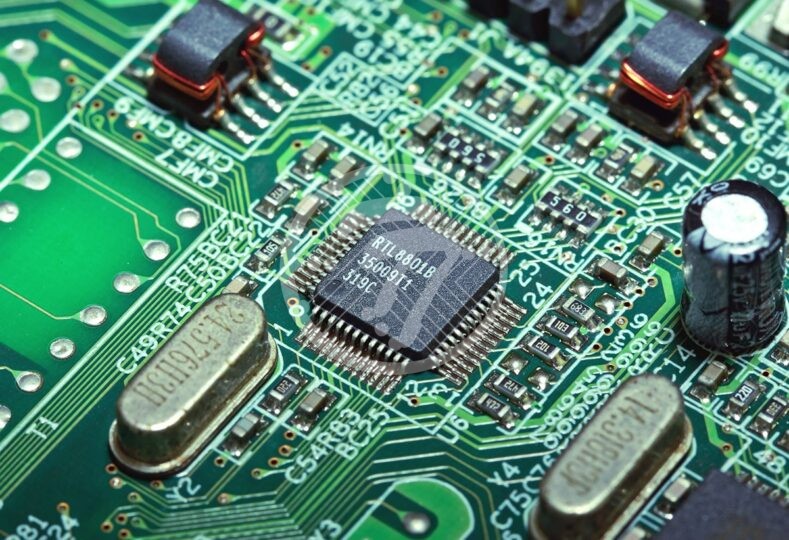
This article gives a clear steer as to the issues related to moisture in printed circuit board. It is a precise write up on reducing the level of impact of moisture on any type of printed circuit board. Right from the Material melds, pcb layout, prototyping, PCB engineering, assembling to packaging and order delivery stage, the effect of moisture in PCB fabrication should be taken care of to avoid damages and other issues in the functioning of the PCB. Furthermore, let’s take a dip into significant measures implemented for controlling the humidity level during the process of lamination, at the time of PCB assembly and controls implemented during storage, packaging and shipping of order.
Rigid/Flex printed circuit board assembly, cable harness, box-build assembly or wire harness PCB assembly are fabricated with varied types of material meld that well suits the attributes required for strong mechanical and electrical capability in electronic products that are used in all dominant sectors globally. Be its need for high frequency with low impedance, compact, durable, high tensile strength, low weight, multiple feature, temperature control or resistance to humidity, the PCB is categorized as single layer, double layer or multi layer depending on the complexity of the circuitry. Among all the serious concern that should be taken care from the initial stage of PCB manufacturing, humidity or moisture is the prime element that becomes the cause of creating a room for electronic and mechanical disorders in the PCB operations.
How moisture can create a great fuss in printed circuit boards?
The moisture can forge ahead various defects in the PCB assembly by its presence in epoxy glass prepreg, diffused in PCB during storage process, absorption at the time of wet processes in PCB manufacturing, residing in the micro cracks or can make a home in resin interface. As the high temperature and vapor pressure go parallel with led-free mechanism in PCB assembly, it results in uptake of moisture level. Check out the guide on How to Protect PCB from Moisture in Outdoor Environments.
Along with the adhesive and cohesive malfunctions in printed circuit boards resulting in Delamination or Cracking, moisture can make the metal migration possible that can cause low impedance path with variation in dimensional stability. With more technical damages like reduction in glass transition aridity, rise in dielectric constant and many more, it results in lower speed of circuit switching and high level of delay in propagation times.
The major effect of moisture in PCB is, it reduces the degree of quality of metallization, lamination, solder mask and the process of PCB manufacturing at large. The limit of thermal stress goes in excess with the reduction of glass transition temperature due to the effect of moisture. Sometimes it also leads to critical short circuits with the effect of moisture ingress that results in ionic corrosion. The other common attributes to moisture absorption in the printed circuit board assembly includes Blistering or Delamination, increases the (DF) dissipation factor and (DK) dielectric constant, thermal stress on plated through hole and oxidization of copper.
Ways to mitigate moisture in PCB fabrication:
Whether the PCB fabrication uses simple or complex technologies, there are many operations in PCB engineering that requires a wet process and also removal of residual moisture. The raw materials used in PCB manufacturing need protection during storage, handling and tackling stress during PCB assembly process. A short guide to controls implemented at the time of various stages of PCB operation is addressed below:
1. PCB Lamination
Lamination is a dehydrating step in PCB fabrication as the cores and prepregs are stacked with bonding the layers into the laminate. The chief elements to control in the process of lamination is the degree of temperature, time taken and heating rates. Sometimes with low aridity, the steps are taken to decrease the magnitude of vacuum to lessen the chance of internal voids that attracts the humidity to get absorbed. So the degree of moisture can be well controlled with using gloves in handling the prepregs and that too from the edges. This reduces the cross contamination. Non corroding humidity indicator cards should have flexibility to resolve the humidity levels whenever required. The wash cycle of laminates should be of short duration with effective storage in a controlled environment which helps prevents the forming the pockets of humidity in laminates.
2. Post lamination processes and PCB assembly
After the drilling, photo imaging and etching operations in PCB fabrication, the moisture absorption rate is higher as it gets entrapped during the wet processes. The silkscreen cure and solder mask bake are steps that are processed to get relief from the entrapped humidity. This adds up to more effective in reducing the level of moisture uptake by minimizing the holding time interval between the steps and even keen in managing the storage conditions. By ensuring at the early stage of PCB lamination that circuit boards are sufficiently dry can help reduce baking operations after lamination. Also, using a high quality surface treatment to prevent cracks during drilling and removing the residue humidity by baking before the process of hot air solder levelling. The baking time should be kept by considering the decided level of moisture content, complexities in the PCB fabrication, PCB finish and adequate thickness required in the circuit board.
Thus, it is vital to get updated on the effect of moisture in PCB fabrication to avoid malfunction, damages and short circuit on the PCB with increasing the cost of rework as well. Researches are now upcoming with more advanced solution to control the element of moisture in each and every step in PCB manufacturing that saves time, energy and cost by using environmentally friendly PCB technologies.
Technotronix has a combined and extensive years of experience in PCB engineering, prototyping, PCB Making, assembly process and PCB fabrication. Having a strong customer base from different sectors, they have a well defined Fabrication Unit with the high tech tooling room. Our team of skilled engineers have experience in tackling and providing an optimum solution to any king of printed circuit board project. Here at Technotronix, we proffer high end customization to address the exact needs of electronics manufacturers. Be it lamination, drilling, prepregs, solder mask, through hole or any simple or complex process, we have stringent testing modules to avoid damages, defects in batch of production.
Please explore our PCB Assembly services. Feel free to contact us to get consultancy, quote or to get updates on our recent project. You can simply drop an inquiry to [email protected] or give us a call at 714/630-9200 to solve your queries.
Get a Quick Quote for PCB Assembly services!