How to create precise PCB assembly drawing quickly and efficiently?
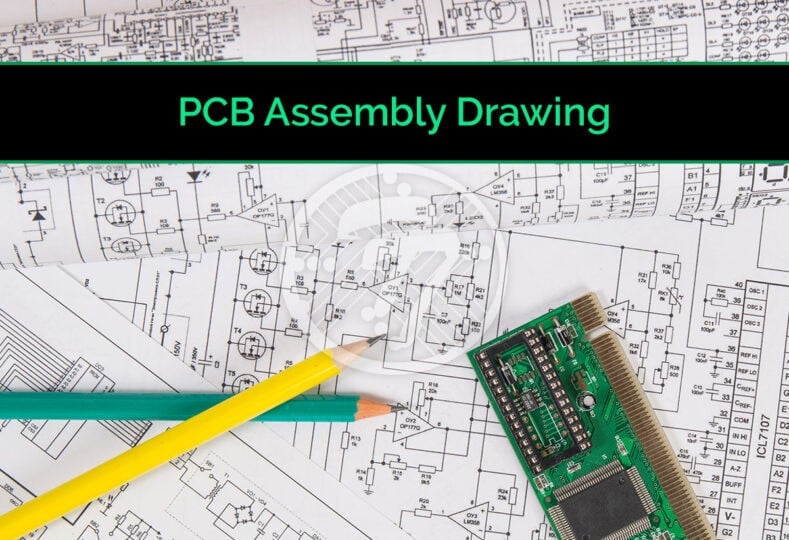
Precise PCB assembly drawings are the key to success for a PCB project. With detailed drawings, it is that much easier to get the exact output that you have envisaged. In creating these drawings, however, need you to keep a number of important aspects in mind:
PCB Assembly Drawing
1. Bill of Materials
A very important component of your design is the Bill of Materials. Among other things, it goes a long way in making available the component shapes and reference designators on the board that makes the assembly process seamless. You will also need to include mechanical parts that may need to be attached to mounting hardware. Besides the drawing needs to identify the exact components required as well as the materials. Manufacturing labels need to be identified as also referenced in the notes.
Some of the best practices to follow when a metal element needs to be used, for example, include:
- Specify the metal to be used.
- Specify the finish that the metal needs to have.
- Specify whether it needs to be painted or powder coated.
It is also prudent to include additional views. The double-sided boards, for example, will benefit from providing a view of the front and back of the board. Also, where mechanical parts are being added, expanded views will help provide clarity.
The more details you provide, the more the board will live up to your specifications. As they say, “God is in the details!”
2. Specify the dimensions
It is imperative that all dimensions are specified in detail. To do that, it is best to use a CAD program. A board design software such as Altium or PADS works well.
In a wiring diagram, it is also important to demonstrate the connections for custom cable assembly as well as the type of termination that needs to be used.
The use of the right software makes sure there is precision & the final assembly lives up to your specifications.
3. Ensure you attach relevant files
When it comes to PCB assembly, it is essential for the contract manufacturer to have the following files:
- Gerber Files
- Drill Files
- Silk Screen Files
- Placement & Drawings Package
Ensuring that the assembler has the exact details of where the holes need to be drilled and where the components need to be placed will ensure success of assembly.
4. Detail the testing requirements
It is important also to think through the testing at the outset and indicate the same to the PCB assembly partner. That way there are no rude surprises at the end.
In fact, it is extremely important to specify to the contract manufacturer whether you will be requiring programing. In which case, the programming files will need to be included and the exact programming will need to be specified.
5. Any special PCB assembly drawing requirements
You also need to think through any special requirements of your project and add a quick note in the drawings. Some examples of the special requirements to be mindful of, include:
- Whether you require lead free assembly.
- Any special requirements when it comes to packaging of the product.
- Export documents that are required, in case the product is being exported.
- Any other Assembly notes that could include industry standards and specifications, special feature locations & more.
To sum up
While a lot of these details go in to successful PCB assembly of the board, you may also find the process daunting. The good news is that there are PCB design systems available that use automation to create drawings. These tools go a long way in saving time and energy while ensure that the drawings are extremely robust. In short, these tools with their powerful automation help you create PCB drawings, both quickly & efficiently.
The choice of the right PCB contract manufacturer is also extremely crucial in making your PCB assembly process, a success. Armed with experience and industry best practices, they ensure that you do not have to reinvent the wheel. Any flaws in the design are pointed out by their engineers in the early stages saving you from costly errors that accrue from discovering these issues once the product is ready to be shipped, or worse still when it has already hit the market.
Technotronix offers professional PCB Assembly services with 40 years of expertise. Our accurate PCB assembly process meets the quality standards, including ISO-9001:2015, RoHS, and more. If you have any questions or any requirements related to PCB assembly service, please feel free to contact us via email at [email protected] or call at 714/630-9200.
Request PCB assembly quote for your any type of requirements.