In-Circuit Test (ICT) vs. Flying Probe Test: Which one is best for your Electronic Board Assembly!
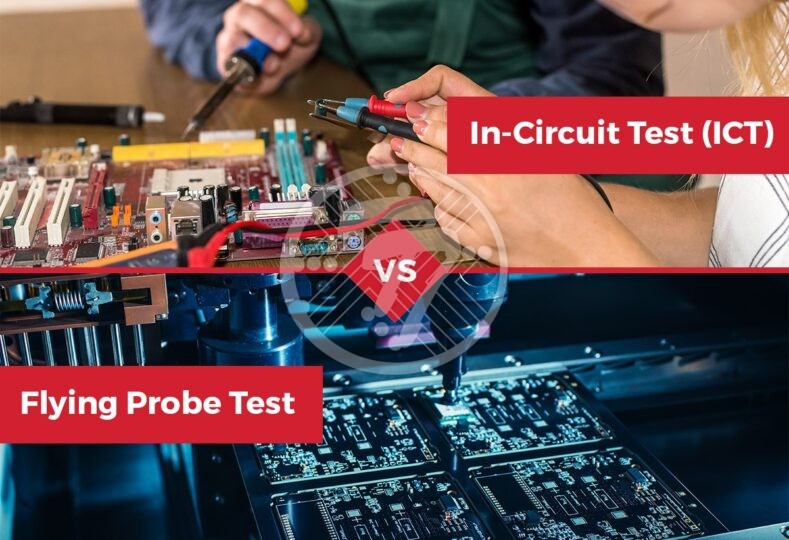
When it comes to making a decision about the best testing method for your PCB, they are a number of factors to consider. Some of these include:
- Costs- both up front as well as per unit
- Coverage
- The lead time involved
- Customization
- Whether or not it suits the complexity of your design
While both the tests are equally equipped to discover defects such as opens, shots, resistance, capacitance, and component orientation, their differences lie in the following areas:
- Development Time involved
- Coverage
- Costs per unit
- Custom tooling
- Engineering charges
Let us take a detailed look at In-circuit vs Flying Probe testing on these criteria as also determine which is most suited for your electronic board assembly.
In-Circuit Testing
The way In-circuit testing or ICT, as it is popularly known works, is that it uses a bed of nails to access the circuit nodes and then check the performance of each component. It can also test the functionality of digital circuits, however, the cost involved there is substantial.
Typically, the strength of ICT lies where you need to test products that are high volume. It is also useful in testing well-developed products. However, since ICT requires that a custom fixture be created, the costs involved as well as the lead times are high. However, the advantage of ICT lies in the fact that once you have the custom tool ready, the per unit costs are low.
If we were to summarize the Pros & Cons of ICT, they would look as under:
Pros
- It lends itself to quick tests per PCB unit.
- The per unit costs are low.
- It can test individual components.
- It works well when you need to test logic functionality.
- It can be used to test LED components.
- You can use it to test BTC component soldering by way of a pressure test.
Cons
- The lead time involved in development tends to be long, which can be an issue in today’s times where a quick go-to-market is a source of competitive advantage.
- The high up-front cost can be detrimental in its usage.
- It requires the use of programming tools.
- You cannot use it to test either non-electrical components or to test connectors.
- While it can be used to test individual components, it does not lend itself to testing components working together.
Flying Probe Testing
FPT (Flying Probe Testing) uses both movable and fixed probes to test the top and bottom of your PCB. It uses high-precision needles, which are programmed to undertake electrical and PCB functional tests.
As a thumb rule, Flying Probe Testing works well for low-volume orders. It is also suitable for products that are in the initial stages of development. Since it does not require custom tooling, the costs of FPT, work in an inverse manner as compared to ICT. So, FPT has higher per unit costs as opposed to high up-front costs of ICT.
Let us look at the Pros and Cons of using FPT:
Pros
- It does not require any custom tooling saving upfront costs and time.
- You do not have to waste precious time in programming.
- It is best used to test components individually.
- It can be used to test LEDs.
- It has low upfront costs.
Cons
- The per unit costs are high.
- It cannot test connectors as well as non-active components.
- While it can test components individually, it is not suited to test components working together.
Which works better, ICT (In-Circuit Test) or FPT (Flying Probe Test)?
There is no one-size-fits-all when it comes to the choice of ICT or FPT. The choice truly depends upon your individual project requirements. You need to look at factors such as whether you want to go in for low volume or high-volume testing, what kind of lead times you have available, your overall budget as well as the complexity of your PCB design in coming to a well-thought-out decision.
It is important to discuss each of the options with your electronic contract manufacturer. It is imperative that the PCB contract manufacturer you are working with has a complete understanding of each test system and can advise you on which one will work best for your specific needs.
Technotronix is one of the leading printed circuit board manufacturers based in the USA. We have over 4 decades of experience in providing innovative PCB manufacturing services using modern technologies and the latest machinery. We are adhering to strict high-quality standards and compliant with the RoHS (Restrictions of Hazardous Substance). To know more, please contact us.