What are the design considerations and guidelines of round circuit boards?
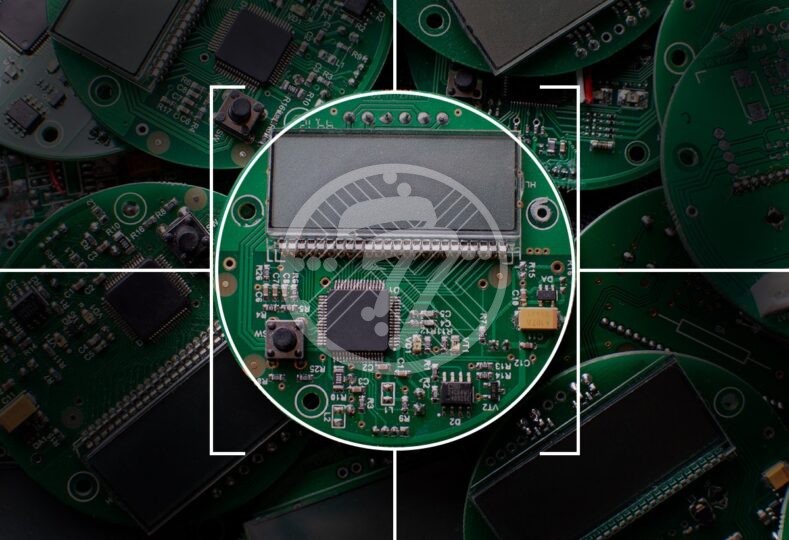
Today, PCBs are available in a wide range of shapes, even though square and rectangular PCBs remain the most common. With the ever-developing electronics industry, the one shape that is gaining prominence is round PCBs.
As the name implies, a round circuit boards is a PCB that comes in a circular shape. It is often used in consumer electronics, wearable devices and more.
The advantage with round PCBs is that it offers increased board space. Fabrication of round PCBs however requires a lot of care since it is a complex process. In fact, the routing process of a round PCB requires a lot of time. All of this also has a repercussion in terms of the overall costs of round PCBs.
Types of Round PCB
Round PCBs, in turn, are of different types. These include:
- Single-sided PCBs
- Double-sided PCBs
- Multilayer PCBs
A single sided round PCB comes with one conductive copper layer. This type of PCB is extensively used in low-density designs. Such a PCB has components on one side of the board while there is a conductor pattern on the other side. Such PCBs use either through-hole or surface mount technology.
Double-sided round PCBs have conductive layers on two sides of the board. They are extensively used when it comes to applications such as wearable devices, lighting systems & more.
A multilayered round PCB has more than two conductive layers. Even though they are the hardest to fabricate, they offer multiple advantages including:
- They lend themselves to higher density.
- They offer increased board space.
Round PCB Design
It is a given that round circuit boards are more complex when it comes to the design bit. Thankfully though there are few tools available that aid the design of a round PCB. There are several design rules, however, that need to be followed when it comes to round circuit boards. For example, the perimeter of such boards can only be shaped with a straight-line segment. Also, in arranging the lines of the perimeter, a circle needs to be placed on the silkscreen layer. Let us look at some more PCB layout and design rules in detail:
Round Circuit Board Design Rules
- First & foremost, when using the CAD tool, it is important to draw the shape in the CAD tool.
- Of course, if the round circuit board is being designed for a high-speed appliance, your choice by default will have to be a multilayered printed circuit board.
- The power and ground planes need to be defined in separate layers. A polygon editor can go a long way to define the shape of ground or power planes.
- Some software also offers the option of customizing the power & ground planes.
- What also needs to be kept in mind is that round circuit boards need panelization schemes for their design.
- To panelize a round PCB, break routing is widely used. It is imperative that a 10 mm (about 0.39 in) clearance is kept between the round circuit boards. With a larger routing tool, however, the clearance can be increased.
- As far as the mounting technology goes, both SMT (Surface Mount Technology) as well as THT (Through Hole Technology) can be used to place components, although SMT is better suited.
To sum up
Overall with Round PCBs, designers have a lot of flexibility. The added advantage also is that there is the possibility to incorporate more features as you go along. Also, with the help of CAD tools the designer can add pad shapes in the circuit board.
While such boards are complex to design, the use of the right software can aid the designing process. Following design rules & best practices can also go a long way in making eth process seamless. It is also imperative that you deal with a professional electronics contract manufacturer who is involved in the PCB design phase itself. That way, the manufacturer can assist you with the best practices & point out any design flaws early, so that you do not have to contend with any costly issues at the fabrication stage. Needless to mention that design issues once the board is manufactured can sometimes even lead to irreparable damage to a company’s reputation.
At Technotronix, we are fully equipped to handle your PCB manufacturing requirements. With over four decades of experience in delivering high-quality, on-time, competitive price products, you can rely on us for your PCB requirements. In case you have any questions, please feel free to contact us via email at [email protected] or call us at 714/630-9200