EV Charger PCB Assemblies enhance safety, efficiency, and reliability!
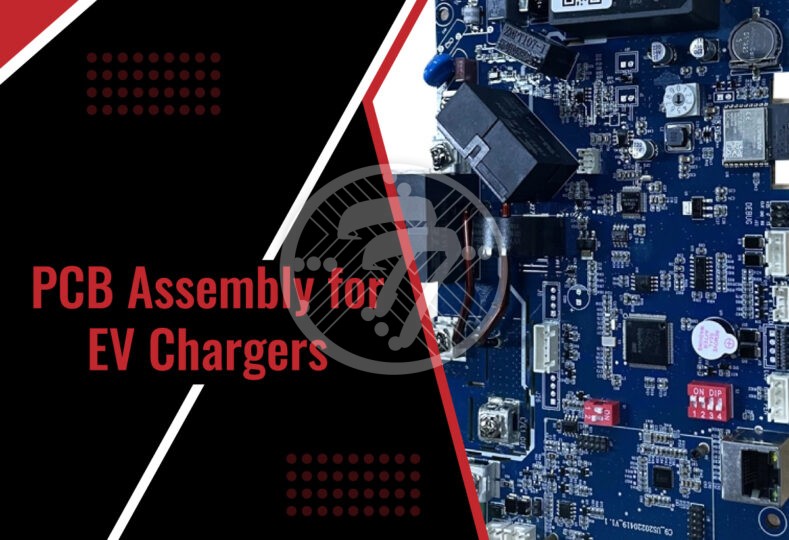
With the rising popularity of electric vehicles (EVs), there’s a growing need for better charging solutions. This surge in demand has put a spotlight on the production of Electric Vehicle (EV) chargers, specifically focusing on the essential role of Printed Circuit Board (PCB) Assembly. This process involves creating the necessary components crucial for efficient EV charging systems. This article will explore the importance of EV Charger PCB Assembly, explaining how these specially designed circuit boards are vital for making electric vehicle chargers work effectively.
What is an EV Charger PCB Assembly?
EV Charger PCB Assembly refers to the process of designing, manufacturing, and assembling printed circuit boards (PCBs) specifically tailored for electric vehicle (EV) chargers. These PCBs are integral components in the construction of EV chargers and play a crucial role in their functionality, performance, and safety. EV Charger PCB Assembly involves meticulous design, manufacturing, assembly, and testing processes to ensure the production of safe, functional, and compliant PCBs integral to the performance of electric vehicle chargers. All the information about the EV charger PCB is discussed below.
Designing the EV Charger PCB:
The design phase of an EV charger PCB is pivotal as it determines the PCB’s ability to handle high power and voltage levels, accommodate numerous components, and ensure safety compliance. Key considerations in the design phase include:
- Circuit Complexity: EV chargers comprise complex systems necessitating PCBs capable of managing the safety of the charger.
- Safety Features: Meeting stringent safety standards requires incorporating safety features such as fuses, surge protectors, and ground-fault protection into the PCB design to ensure user safety.
- Heat Dissipation: Thermal management is crucial due to the generation of heat from high-power levels. Effective design strategies prevent overheating and ensure optimal performance.
- Signal Integrity: Maintaining high-speed data transmission integrity is essential for effective communication between the charger and the vehicle. Designing the PCB to minimize noise interference is critical.
Manufacturing and Assembly Process:
The production of EV charger PCBs involves
- PCB Layout: This stage involves designing the physical layout of the PCB, including component placement, trace routing, and incorporating markers for easier manufacturing and assembly.
- Printed Circuit Board Manufacturing: After the layout is finalized, the PCB fabrication process begins. This process, conducted by specialized manufacturing facilities, involves etching a pattern onto a copper-clad substrate to create the desired circuitry.
- PCB Assembly: The assembly process involves attaching electronic components to the PCB. Two primary techniques are used:
- Through Hole Technology (THT): Components are inserted into drilled holes on the PCB and soldered on the other side, suitable for larger components requiring additional mechanical support.
- Surface Mount Technology (SMT): Components are directly mounted onto the PCB surface, reducing size and accelerating assembly.
Quality control during assembly ensures proper alignment and soldering, crucial for the safety and functionality of the final product.
Testing Procedures:
After assembly, rigorous testing is conducted to verify safety and functionality. Key testing procedures include:
- Electrical Testing: Checking circuit continuity to ensure proper power flow throughout the PCB.
- Functional Test: Verifying proper functionality and meeting performance requirements of the EV charger.
- Safety and Compliance Testing: Includes Hipot (High Potential) testing, environmental testing for varying conditions, EMC testing, and compliance with safety standards (such as IEC 61851, ISO 15118, SAE J1772, IEC 62196).
Outsourcing and Reliability:
Outsourcing PCB assembly for EV chargers is common. Working with experienced assembly providers, adhering to industry standards, selecting high-quality components, and conducting thorough testing ensure reliability and quality.
What Are the Safety Considerations for EV Charging?
Safety considerations for EV charging are crucial to prevent fire hazards and electric shock injuries. Here are key safety measures to adhere to while charging your electric vehicle:
- Qualified Installation: Before purchasing an EV, have a qualified electrician install a new, dedicated circuit suitable for EV charging devices. Ensure older home wiring is assessed for compatibility.
- Charging Device Certification: Use charging devices certified by nationally recognized testing laboratories. Follow the manufacturer’s guidelines for charging, especially for Level I, Level II, or DC fast charging.
- Proper Outlet Usage: Plug Level I EV chargers directly into outlets designed to handle their amperage. Avoid using multiplug adapters or extension cords. If an extension cord is necessary, ensure its heavy duty and rated for outdoor use.
- Residual Current Device (RCD): Install an RCD with the charging unit to detect faults and cut off power, reducing fire risks.
- Child Safety Measures: Keep all charging components out of children’s reach when not in use to prevent accidents.
- Regular Maintenance: Follow manufacturer maintenance guidelines and regularly inspect charging components for wear or damage. Never use damaged EV chargers as they pose a potential shock hazard.
- Protection from Elements: Protect the EV charging station outlet from water ingress and follow manufacturer guidelines for safe charging in wet conditions.
- Certified Charging Stations: Opt for certified charging stations that meet safety standards to prevent overcharging and overheating, ensuring safer charging practices.
- Temperature Consideration: Avoid charging in extreme temperatures (below freezing or above 100 degrees Fahrenheit) as it can damage the battery and reduce its lifespan.
- Cable Inspection: Before charging, inspect the charging cable for any signs of damage. Refrain from using a damaged cable to prevent electrical hazards.
- Prevent Overcharging: Avoid overcharging, as it can negatively impact battery life. Monitor the charging process and aim to maintain the battery status between 20% to 80% for optimal longevity.
- Regular Usage: Use the EV regularly to maintain its health. Prolonged periods of inactivity can impact various components, including the battery pack.
Adhering to these safety considerations is crucial to ensure the safe and efficient charging of electric vehicles while minimizing potential risks of fire, electrical hazards, or damage to the vehicle’s components. If there are any uncertainties or concerns regarding EV charging safety, consulting a certified electrician or the vehicle manufacturer for guidance is advisable.
Conclusion
In conclusion, the significance of the Electric Vehicle (EV) Charger Printed Circuit Board (PCB) Assembly in the realm of electric vehicles cannot be overstated. This process stands as a crucial foundation in the development of components necessary for the efficient operation of EV charging systems.
At Technotronix, we are fully equipped to handle PCB Assembly requirements. We follow industry best practices to ensure we deliver cutting-edge products. Our team of experts and state-of-the-art manufacturing facility ensures that all our PCBs meet the industry standards of quality and testing.
If you have any questions or any requirements related to PCB assembly, please feel free to contact us via email at sales@technotronix.us or call 714/630-9200.