What is the Need of Chemical-Free PCB Fabrication & PCB Assembly?
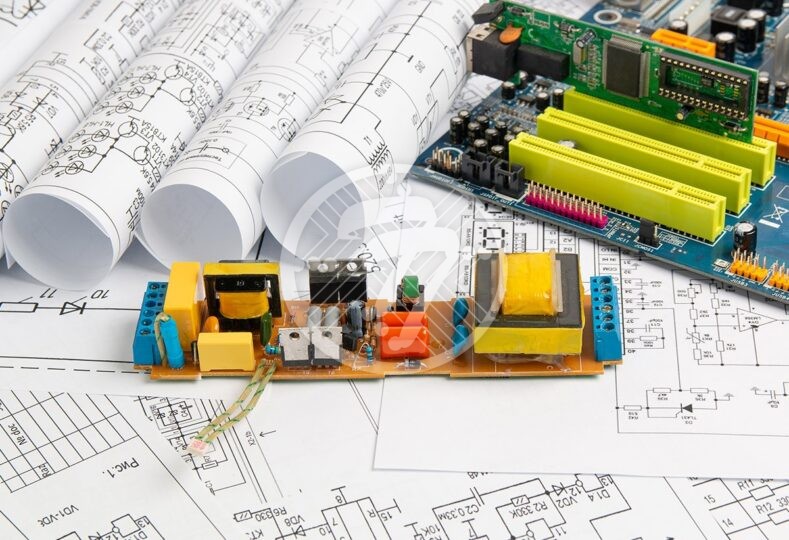
Commonly referred to as PCBA, printed circuit board assembly refers to the process of rigidly mounting electronic components onto a printed circuit board. It is essentially a mechanical assembly process of soldering or assembling disparate electronic components onto one printed circuit board in a manner that enables packaging. A fully functioning PCB is by no means a finished product; it needs to be connected to a power source as well as a display monitor for displaying information. PCB assembly is not generic; they are assembled as per detailed specifications related to the placement of connectors, mounting boards, etc. In many specifications the specifications are detailed enough to require a drawing of the exact location and dimensions of each external component, for instance specifications related to height or keep out areas need to be defined and designed before the fabrication and assembly process itself.
It is common to confuse PCB assembly with PCB manufacturing; the two are completely different and distinctive from each other. Manufacturing PCB’s requires Making and prototyping before actual production while assembly requires soldering of electronic components onto the circuit board for use in a variety of gadgets and equipment. There are many materials required in PCB fabrication and assembly, the primary ones being:
- Printed Circuit Board
- Electronic components
- Soldering materials, including solder wire, solder paste, solder bar, solder preforms (depending on the type of soldering to be done)
- Soldering flux
- Soldering equipments including soldering station, wave soldering machine, SMT equipment, inspection and testing equipment etc.
By the late 1900’s, the threat to the earth’s ozone layer posed by emissions from CFC based defluxing solvents like Freon and Trichloroethylene brought about a renewed focus on the need to reduce the use of chemicals in manufacturing. The increased clamoring led many organizations to abandon CFC based defluxing solvent sin favor of aqueous based defluxing as well as no clean fluxes. The standards of defining green technology have evolved considerably since then, also because of regulatory directives which have made it imperative for companies to adopt cleaner chemical free PCB fabrication and assembly. Organizations are increasingly looking to adopt methods that reduce product liability as well as environmental liability as a means of bringing down their carbon footprints.
Taking care of the environment
Environmental concerns aside, safety in the workplace also becomes paramount not only during process operations, but also with regards to performing routine cleaning and maintenance functions, which are why many environmentally committed organizations have started adopting lead free soldering, even though it sells at a 200-300% premium. It is not just workers in factories where PCB assembly takes place that are susceptible to exposure from toxins released during the process, but even the end consumer purchasing these products.
Environment friendly PCB cleaning processes
It is in the cleaning process of PCB assembly that chemicals are chiefly used, although there are many industries that require use a no-clean process. However, industries like aeronautics, automotive and medical industry do require post assembly cleaning of solder reside paste. It is these industries that have demanded that manufacturers of PCB fabricators and assembly adhere to chemically reliable cleaning solutions that are also environmentally friendly. The European Union already has strict guidelines regarding chemical free fabrication and assembly of PCB’s. The ROHS directive is very clear in its stipulations that, from July 2006 onwards, member states are required to ensure that new electrical and electronic equipment released in the market should be free of lead, mercury, cadmium, hexavalent chromium, PBB or PDBE. Since the ROHS Circuit Board guidelines are a product based initiative, the responsibility for compliance lies with the manufacturer. This means that from an environmental perspective, flux and solders paste residues commonly used for high reliability and long lifecycle PCB assembly products need to be compatible with solvents and detergents required to clean them.
The normal environment that we live in is already rich in pollutants which are why it has become even more imperative to ensure that we do not add to the contamination by adopting manufacturing and assembly processes that do away with using any kind of harmful chemicals. While there is no regulatory body in the US for testing of PCB Fabrication and Assembly processes, the government has come out with initiatives that make it mandatory for organizations to use non lead based products in their fabrication and assembly process. Apart from the government based initiatives there is an increasingly active role played by nongovernmental environmental agencies to raise awareness about the safety hazards posed to workers and consumers by the use of chemicals in PCB fabrication and assembly without sacrificing on quality or reliability. Even organizations now prefer working with PCB assembly suppliers who are committed to implementing advanced processes and using high quality raw materials that reduce environmental contamination and provide an increased level of health and safety to workers and consumers.
TechnoTronix is one of the kingpins in delivering a Chemical-Free PCB Fabrication & PCB Assembly service to the electronics manufacturers. Our main strength lies in the extensive experience and skilled team of experts to provide tailored electronic design and manufacturing solution. You can drop an email to [email protected] or give us a call at 714/630-9200 to solve your queries or to get a quote.